This industry-first milestone increases bottom nozzle debris resistance from 65% to 96%
In an industry first, Westinghouse Electric Company used additive manufacturing (AM) to fabricate bottom nozzles that improve debris capture and fuel endurance within its fuel assemblies. The nozzles were integrated into four Lead Test Assemblies delivered to Alabama Power’s Joseph M. Farley Nuclear Plant operated by Southern Nuclear, in the first quarter of 2024.
This press release features multimedia. View the full release here: https://www.businesswire.com/news/home/20240626863181/en/
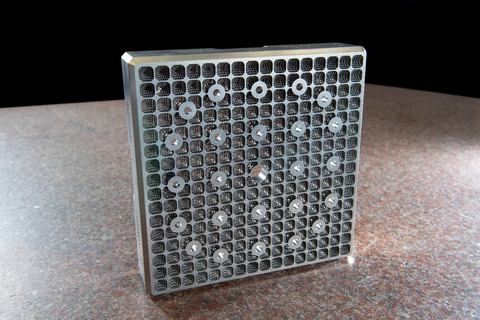
Image of a Westinghouse fuel assembly bottom nozzle fabricated using additive manufacturing. (Photo: Business Wire)
Debris-wearing action on the fuel rod cladding – known as debris fretting – is the primary source of leaks in Pressurized Water Reactor (PWR) fuel assemblies. AM technology offers significant improvements in debris filtering thanks to enhanced design freedom which reduces the diameter of debris that can enter into the reactor. In testing, the additively manufactured components demonstrated a 30% improvement in debris resistance.
“Over the past decade, Southern Nuclear has led the industry in the development and implementation of new technologies that improve fuel resiliency,” said Southern Nuclear President Pete Sena. “The existing nuclear power fleet is the backbone of our country’s clean energy supply, and we are innovating nuclear fuel today to be more robust in order to deliver safer, more affordable, and more reliable carbon-free clean nuclear power for decades to come.”
“Our additive manufacturing technology is allowing us to achieve breakthrough performance with an immediate positive impact for our customers,” said Tarik Choho, Westinghouse President of Nuclear Fuel. “This significant technology innovation for PWR reactors mitigates the risk of leakage in the fuel rods due to the accumulation of debris, strengthening the safety and efficiency of our customers’ operations.”
This milestone demonstrates Westinghouse’s leadership in the nuclear industry to achieve cutting-edge solutions using AM techniques. In 2015, the company conducted the first-ever material irradiation study of AM nuclear components. In 2020, Westinghouse installed the first-ever safety-related AM component, a Thimble Plugging Device, into an operating commercial reactor, and in 2024 Westinghouse produced the 1,000th Additive Manufacturing Component for VVER-440 Fuel.
Westinghouse Electric Company is shaping the future of carbon-free energy by providing safe, innovative nuclear and other clean power technologies and services globally. Westinghouse supplied the world’s first commercial pressurized water reactor in 1957 and the company’s technology is the basis for nearly one-half of the world's operating nuclear plants. Over 135 years of innovation make Westinghouse the preferred partner for advanced technologies covering the complete nuclear energy life cycle. For more information, visit www.westinghousenuclear.com and follow us on Facebook, LinkedIn, and X.
View source version on businesswire.com: https://www.businesswire.com/news/home/20240626863181/en/